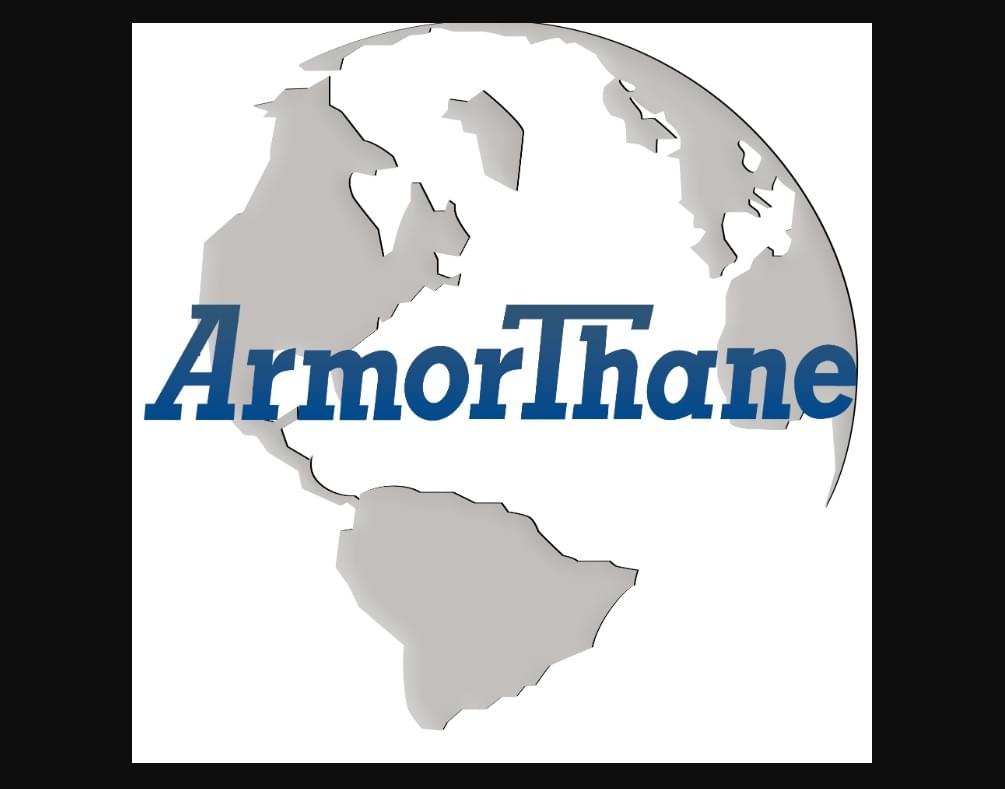
Installing polyaspartic coatings is quite a bit distinct from installing other polymer coatings. Not merely do polyaspartics tend to have shorter working time than other coatings, nonetheless they should be merged and staged differently. Acquire more information about polyaspartic coatings
To assist make sure your tasks concerning polyaspartics can be a accomplishment, it is crucial that you understand these differences. Think about the subsequent before your next installation:
Polyaspartic has a opposing response to epoxy coatings when it comes to pot life and working time. Which means polyaspartics will require much longer to gel in a container plus a quicker time for you to set after they are put out. In the course of application, put out only the maximum amount of product as your crew can reduce in and fully implement within a few minutes so you don’t lose the damp benefit.
Do not enable your “cutter” to work very far in front of the major floor applicators. It is a standard training among epoxy installers to perform the slicing in / benefit work well ahead of the staff working the squeegee and finish roll. Using the faster set duration of the polyaspartic, the product across the corners will start to cure before all of those other crew grabs up when your cutter will get past the boundary forward. That means you won’t have the ability to work the remainder of the material into the pre-minimize ends, making a apparent seam or difference in texture and density between the major floor and also the ends.
Make use of a small squeegee. A 12”- 18” squeegee usually takes just a little longer, but it will abandon less “bird baths” than a 24”+ squeegee. The squeegee individual has to set the application density of your polyaspartic rather than rely on the roller to redistribute the coating. Counting on the roller to generate the done fullness will bring about over-rolling along with an unequal look.
Do not squeegee the ribbon of drenched material down to practically nothing. Doing this will leave an improvement in cured gloss. Remember to keep a small pool of damp material while watching squeegee. And, always begin the ribbon fill from the next combine in the wet material that you are now working.
Set up your workflow to support the faster environment material. If you get the chance, considering the shape of your place you are working in, try and squeegee in the quicker aspects of the room and finish roll in the lengthier sides in the room. This implies if you are working within a rectangle room, the squeegee ought to be going to and fro parallel to the shorter ends from the room (making more, but reduced passes by). The roller must be working parallel on the longer aspects in the room (making fewer, lengthier moves together with the complete roller). This method permits the material to get accomplish rolled faster after it is located.
Do not attempt to install as being a one-person band! Even over a smaller size job, like a residential garage, the staff ought to have at least several applicators. Far more team members must be included on because the square video footage boosts or the level of reducing improves.
Remember that higher humidness will increase the set duration of polyaspartic coatings. It’s not merely the hotter weather you have to think about. Comparable dampness (RH) can have a large impact as well, necessitating the application process to maneuver much more quickly. Installers should make use of a digital psychrometer or hygrometer on every job prior to installment, during application and when curing. It is important to recognize that increased RH provides a catalyst and may shorten the working time of polyaspartic coatings.
Choose the appropriate ROCK-TRED polyaspartic formula for your jobsite circumstances. Use P-200 when temperatures range from 0° - 40°F, P-100 from 40°-70°F, and either P-50 or P-80 for 55°+. If you don’t have the correct formula and have to mount the coating with a job with greater temperature or in higher moisture, you may wish to do these:
Minimize the blend dimensions to simply just as much product as can be applied before it starts to gel
Amazing the material down just before installation. Do not great it earlier its noted heat ranges on the Tech Data Linens or let it to freeze.